Environmental compliance may weed out smaller garment factories
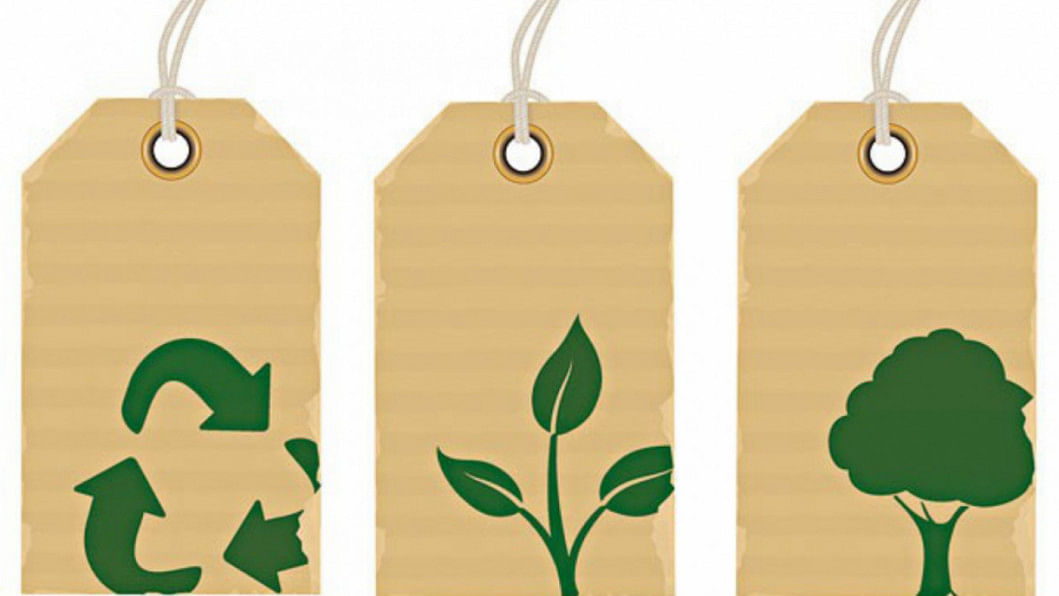
The pressure on supply chains to reduce CO2 emissions intensifies as dates for meeting global climate targets inch closer. There are concerns that CO2 levels are heading in the wrong direction at precisely the wrong time.
Many measures can be introduced to reduce the environmental burden of garment production. The one thing they all have in common, though, is the cost. In some cases, there are exorbitant costs involved. There are several reasons for this. The first is the technology involved. The second is that it is often easier – and more beneficial – to build a completely new factory to the highest possible environmental specifications than to "retrofit" an existing production unit.
It is my firm belief that as global fashion supply chains are "greened" we will see more and more newbuild factories, with access to renewable energy, the latest and most efficient effluent treatment technology, and all other kinds of benefits.
And yet, the cost of a newbuild garment factory is significant. These costs can vary around the world depending on various factors, such as location, size, construction quality, labour, machinery and equipment, and any additional features or requirements specific to the factory. To provide a rough estimate, this cost can range from a few hundred thousand dollars for a small-scale facility to several million dollars for a larger state-of-the-art factory. The latter is what we are looking at and what many of the world's leading garment factories (in terms of reduced environmental footprint) will spend to build.
In Bangladesh, we once had more than 5,000 garment factories. That number has diminished in recent years and I am doubtful as to whether we will ever reach 5,000 again. We have seen smaller operators go bust or find themselves unable to keep up with the pace of change. Sub-contracting has also reduced as buyers have demanded that less production is outsourced to poorly regulated operators. The pandemic also led to some factories falling by the wayside.
The relevance of all this is that it does raise a vital question: will the shift towards sustainable fashion supply chains lead to a corresponding consolidation of the industry? Will we see an industry which has fewer and larger players? In Bangladesh, we once had more than 5,000 garment factories. That number has diminished in recent years and I am doubtful as to whether we will ever reach 5,000 again. We have seen smaller operators go bust or find themselves unable to keep up with the pace of change. Sub-contracting has also reduced as buyers have demanded that less production is outsourced to poorly regulated operators. The pandemic also led to some factories falling by the wayside.
But I also think we could be starting to see a trend whereby garment production becomes more and more consolidated into fewer, larger factories that have the financial clout to meet the highest environmental standards. When one considers this issue logically, it is the only rational way forward.
It is worth pointing out that, in recent years, we have already seen some of the world's largest textile chemical companies merge. Joint ventures and acquisitions have become common in that segment as the cost of regulation makes economies of scale vital.
I expect garment production itself to follow suit. I believe we could see the rise of the super-factory, not just in Bangladesh, but also in other textile production hubs such as India, Pakistan and Vietnam.
Is this necessarily a bad thing? Is it wrong that only the largest players will be in a position to successfully compete while also meeting environmental and compliance issues? I think in the shift towards larger conglomerates, we may lose something along the way in regards to the rich and varied nature of our proud garment industry.
At the same time, size and scale might also bring benefits. Larger players are better structured at an operational level. They might have whole teams in place, whereas smaller factories may have just one person. They are more sophisticated in terms of human resource management, marketing, public relations and legal issues. In short, they have much more in common with the multinational buyers they are working with.
This, in turn, could ensure they are treated more fairly as equal partners than in the past when the buyer-supplier relationship felt unequal and adversarial at times. Another factor is that the more factories you have, the more likely there will be one factory prepared to undercut the rest on pricing issues. As the saying goes, you are only as good as your weakest link. At times, our weakest link(s) has often been our undoing as an industry. The vast, sprawling and often fragmented nature of our garment industry has probably worked against us when it comes to pricing and negotiating with buyers.
By way of contrast, a smaller batch of genuinely world-class operators is arguably a much better fit for our country moving forward. Such an industry will better suited to evolve, innovate and introduce the kind of continuous improvement and best practice programmes that our global client base is increasingly demanding as a prerequisite for doing business.
Mostafiz Uddin is the managing director of Denim Expert Limited. He is also the founder and CEO of Bangladesh Denim Expo and Bangladesh Apparel Exchange (BAE).
Comments