Proper audits can ensure social compliance in the RMG industry
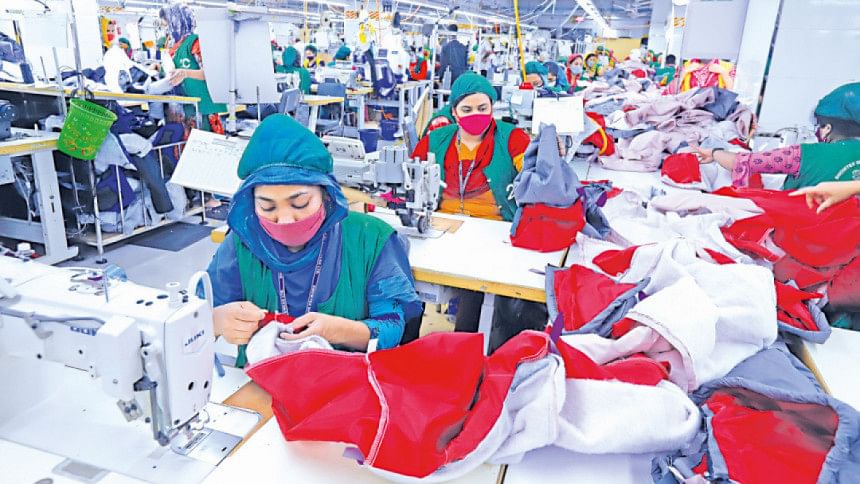
The ready-made garment (RMG) industry of Bangladesh plays a significant role in the country's economy as well as in the global apparel market. The well-being of Bangladeshi RMG workers has long been a topic of concern for stakeholders in the international supply chain. Since 2011, the UN Guiding Principles on Business and Human Rights has served as an ethical compass for global fashion brands and other businesses to protect human rights in the context of business operations. Simultaneously, the formulation of buyers' code of conduct (CoC), particularly in countries like Bangladesh, has had a crucial role in defining guidelines and expectations for suppliers to ensure that they adhere to social compliance standards.
The horrific collapse of Rana Plaza in 2013 further pushed for stricter regulations and much more extensive audit practices to prevent similar tragedies in future. Subsequently, social compliance audits expanded greatly with international brands doing audits of their CoC, and multistakeholder initiatives such as the Business Social Compliance Initiative (BSCI) and Supplier Ethical Data Exchange (Sedex) doing third-party audits.
Social compliance audits are the primary tools to monitor working conditions and prevent human rights abuses in RMG factories worldwide. Most RMG factories experience many audits over the year. These audits seek to secure safety, health, wages, working hours and freedom of association of the workers.
However, audits are expensive for both buyers and suppliers, and overlapping audits from different bodies can cause audit fatigue among RMG factories.
In our research, we have looked at audits in 10 RMG factories as case studies, and the results indicate that despite problems with the current social compliance practices, some factories found ways to achieve benefits from audits.
Factories mainly expressed satisfaction with the audit system, but many compliance managers experienced audit fatigue due to multiple and parallel audits; some also concealed non-conformities from auditors. Generally, audit reports identify non-conformities related to the most visible safety and health issues, such as personal protective equipment, needle guards, and electrical safety, together with issues related to payment and working hours. Ergonomics risk factors such as working postures and heavy lifting as well as freedom of association are rarely included in audits or audit reports.
Workers' voices influence audits to a limited degree. Auditors don't give the workers a real chance to point to critical issues, and if they do, the issues are not necessarily brought to the attention of the management.
The factories we included in our research revealed two different approaches of responding to audit practices:
1) A low road, where the factory considers buyers' and audit requirements as unfair and costly. They believe that cost reduction is the only way to be competitive. Therefore, they go for an absolute minimum standard of compliance, often with elements of window dressing. In this group of factories, we noticed the tendency to make informal arrangements with the auditors. Visits to these factories showed limited investments related to working conditions, but also to technology and operations. Overall, these factories have low management capacity both in general and related to social compliance.
2) A high road, where factories take a systematic and proactive approach, establishing management systems with clear procedures for both operations and social compliance. These factories believe that they can stay competitive through high quality and high productivity developed with a motivated workforce as well as continuous improvement of technology and work organisation. They use audits as a source for identifying additional possibilities for improvement. These factories turned out to be affiliated to the Better Work programme, a flagship initiative of the International Labour Organization (ILO) and International Finance Corporation (IFC).
Our research highlighted that factory management is usually the driving force behind choosing the low or the high road of social compliance practices. Irrespective of the compliance strategy followed, we found that managements as well as the auditors have neglected certain occupational safety and health (OSH) issues encompassing ergonomic demands for workstation design, training in preventive measures, reduction of highly repetitive work and psychosocial climate such as prevention of various forms of harassment.
We propose the following steps to address these gaps:
1) Dissemination of research results and exchange of experience among peer factories.
2) Stronger involvement of buyers and brands in the welfare of workers. One reason for the selection of the low road practice is expression of limited genuine interest in social compliance among the buyers.
3) Inclusion of neglected problems in audits such as ergonomics, workers' voices and stronger quality control of audits to avoid conflicting interests.
Audits should not only rectify current problems but also support the development of a strong preventive safety culture. Our study showed that it is possible for a factory to reach a high level of social compliance and at the same time be fully competitive by using audits to improve conditions for both workers and the business.
This article summarises key findings from a research titled "Social Compliance Audits in the Garment Industry in Bangladesh: Present Practice and Future Perspectives (2024)." The research was conducted jointly by Bangladesh University of Health Sciences and the University of Southern Denmark.
Dr Saika Nizam is project coordinator of Occupational and Environmental Health at Bangladesh University of Health Sciences.
Prof Peter Hasle is project leader of Global Sustainable Production at the University of Southern Denmark.
Sarmin Sultana is PhD student in Occupational and Environmental Health at Bangladesh University of Health Sciences.
Julie Bundgaard is PhD student in Global Sustainable Production at the University of Southern Denmark.
This article summarises key findings from a research titled "Social Compliance Audits in the Garment Industry in Bangladesh: Present Practice and Future Perspectives (2024)." The research was conducted jointly by Bangladesh University of Health Sciences and the University of Southern Denmark.
Views expressed in this article are the author's own.
Follow The Daily Star Opinion on Facebook for the latest opinions, commentaries and analyses by experts and professionals. To contribute your article or letter to The Daily Star Opinion, see our guidelines for submission.
Comments