Use of mild steel rebar in seismic design on RC buildings
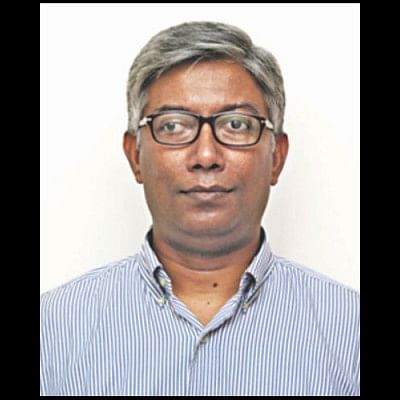
Mild steel rebar, commonly known as MS rod or simply rod, is an essential component of building materials. This product is being manufactured in our country for a long time. Construction of reinforced concrete buildings started in this country approximately after the 2nd World War. The first re-rolling mill to manufacture MS rod was established by the H Akberali Group of Industries at the Nasirabad area of Chittagong named Bangladesh Steel Re-Rolling Mills (BSRM) in 1952. Later it was followed by the establishment of Rahim Steel Mills Ltd. in 1958. In the post-liberation period, more steel mills emerged in the market, notably the Kabir Steel Re-Rolling Mills (KSRM) and Ratanpur Steel Re-Rolling Mills (RSRM), both in 1984, AbulKhair Steel Ltd. in 1991 and many others. All these mills can now meet the internal market demand. Some companies are even exporting rebar to neighbouring countries. From the beginning till the '80s decade, all these mills manufactured rebar of grade 275 (275 Mega-Pascal equivalent to American ASTM Grade 40 or yield strength 40 ksi). There was no national standard for manufacturing rebar that time. Also we had no design code to guide the engineers to properly design the buildings considering the geo-environment of Bangladesh. BSTI first published the national standard BDS-1313 for manufacturing MS rebar in 1991. Two years later, the first edition of Bangladesh National Building Code (BNBC) was published in 1993. BNBC provides adequate guideline for engineers to design and construct buildings considering the weather and geological characteristics of Bangladesh. In BNBC, the whole north-eastern side of the Padma-Meghna River including the whole of Chittagong area has been declared as vulnerable to earthquake. Among these areas, Sylhet, Mymensingh and the northern parts of Dhaka fall in severe seismic vulnerable zone. In these areas, the BNBC code dictates to construct special seismic structural systems for the buildings. Since the 80s, with the economic growth of the country, demand for construction of multi-storied high rise building increased. At the same time, the consciousness for construction of seismically safe buildings started increasing. To meet the demand of high-rise construction, production of Grade 420 (equivalent to ASTM Grade 60) started in the 90s which was also pioneered by BSRM. In 2006, BSTI published a new standard BDS ISO 6935 for MS rebar which is also followed internationally in many European countries. In 2008, BSRM started production of Grade 500 rebar and other companies also followed suit. Recently in 2015, BSRM introduced Grade 420 rebar specially fabricated for seismic application and Grade 550 for large/mega structures in accordance with American ASTM A706 standard. Process of the publication of equivalent Bangladeshi standard BDS ISO 6935 – 2016 is also underway. Such development in the grade of rebar can be observed worldwide.
Water, sand, stone chips, cement and MS rebar are the main ingredients of concrete construction. Seismic resistance characteristics of a concrete structure primarily depend on the properties and arrangement of rebar. Properties of other ingredients generally do not have any contribution to the seismic resistance characteristics of a concrete structure. For this reason, it is necessary for everyone to have some idea about the engineering properties of MS rebar. Especially, for the engineers engaged in the design and construction of concrete buildings, this is extremely important.
From seismic design consideration, the important engineering properties of rebar are a) unit weight –the weight of a piece of rod of 1 m length, b) yield strength – generally the tensile stress level up to which the rod elongates proportionally, c) ultimate strength – maximum stress level a rod can sustain before fracture, d) elongation – the amount of extension a rod sample undergoes in tension before fracture which is generally expressed as a percentage of original un-elongated length, e) bend test – how easily a rod can be bent without breaking and f) deformation measurement – appropriateness of the geometric measurement of the surface patterns of the rod.
For seismic resistant design, the yield and ultimate strength and the amount of elongation is very important. The tested yield strength must be equal or greater than the rated strength of the bar but at the same time it shall not exceed the rated strength by 125 MPa. For example, for Grade 420 rebar, the tested yield strength shall be between 420 MPa and 545 MPa (420+125). The ratio of tested ultimate strength and tested yield strength shall be 1.25 or higher. This is a very important and essential characteristic for specially designed seismic resistant structures and must be ensured before construction. After testing, the total elongation of the broken specimen shall be at least 12% to 14% on a 200mm gage length, depending on the diameter of the rod. Only a few of the brands of MS rod available in the market can satisfy all these requirements. It is, therefore, strongly suggested that the required properties of the rod to be used in a building be tested from reputable and reliable laboratory before being used in a construction.
Fatigue characteristic is another property to judge the quality of steel. Generally speaking, good quality steel must possess the required fatigue characteristic as per the standards. Good fatigue properties are essential for the design and construction of steel bridges like the Hardinge Bridge. However, it must be made clear that fatigue property has nothing to do with the seismic design of concrete buildings. Fatigue property is not required or used in the construction of seismic resistant concrete structures. In the highly competitive market, some of the manufacturers show catchy advertisements mixing up fatigue with seismic design and put people in confusion which is undesirable. Readers are requested not to get confused seeing such ads. Instead, they are advised to seek the opinion of experienced engineers or experts and get the rods tested from a reliable laboratory.
The writer is Professor, Department of Civil Engineering, BUET.
Comments