Are we safe from building collapse?
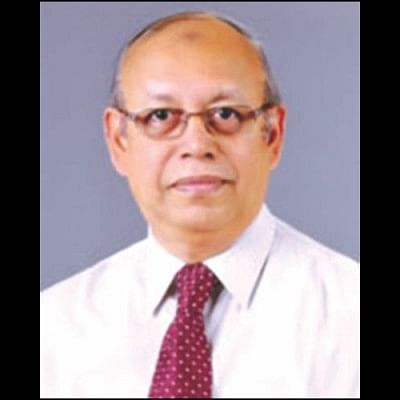
Adevastating tragic failure took place in Savar when a nine storied factory building(Spectra Sweaters Ltd.) completely collapse on April 12, 2005at night when workers were working inside. Sixty persons died and about 100 were seriously injured. The whole incidence shocked the nation and the civic society were vibrant about more stringent regulatory laws and implementation of quality assurance process for all civil engineering structures.
Rana Plaza, located at Dhaka–Aricha highway near Savar bus stand, collapsed on 24April 2013 at around 8:30 am, resulting in 1134 deaths and more than 2500 injuries. Rana Plaza housed five garment factories employing around 5000 people, 300 shops, and a bank. From newspaper sources it is learned that it was a 9-storied industrial building with a single basement. Local Municipality (Savar) gave permission to the owner of Rana Plaza to construct a five storey commercial building with one basement in 2005. Later the owner was allowed to extend it up to nine storey, without considering the structural design, though the foundation of the building was for 5 storey. Moreover, the building was converted from commercial to industrial use, and power generators were placed at the higher floors. As a result of such violation in building construction, cracks developed on some pillars and on few floors of the building following a jolt on 23April 2013, a day prior to the fateful day. After inspection, industrial police requested the building authorities to close the building and to suspend operations of the factories on that day. However, the building owner and top management of the garment factories ignored the warning and forced the workers to work in the next morning on 24April, 2013 .As a consequence, the collapse resulted in the high death toll of 1134 and more than 2500 people were badly injured at the end of the rescue operation on14May 2013. This tragic accident received global attention, and brought forward diverse issues concerning workplace safety and working environment for workers. The employers, brands and consumers – the entire supply chain in the RMG sector was alerted for an acceptable code of construction and design practice for factory buildings.
We have read about a lot of building failure stories that have taken place in the capital city of Dhaka.
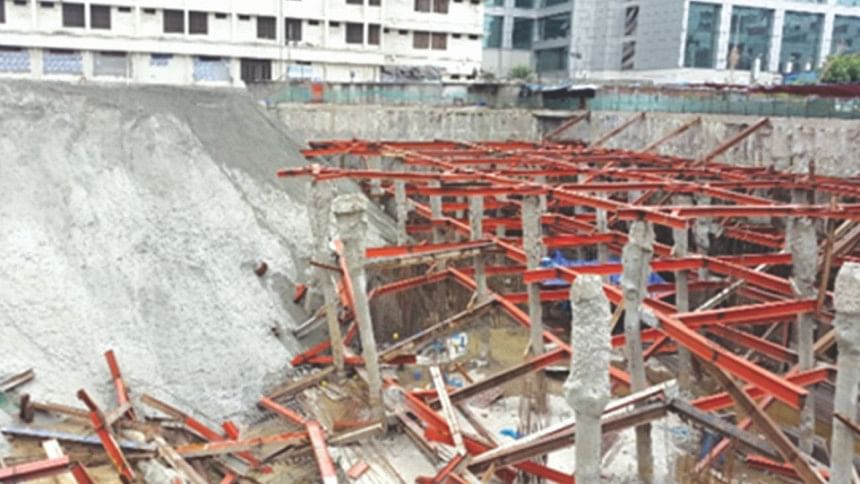
Two decades back a building located in a newly filled land and built on the slope of the fill in Sabujbag area of Dhaka failed when the second story was under construction. The rear columns on foundation footings settled and the whole building rotated. The front columns snapped from the footing resulting in collapse of the building. In Kalabagan a five storied building constructed over a pond filled with earth collapsed when the fifth storey was under construction. Column reinforcements snapped from the footing foundation and the whole building rotated and tilted. A seven storied building in Kathalbagan tilted resulting in collapse of ground floor (soft storey) damaging columns at supports. It is learned that the building was built over a ditch filled with rubbish and foundation consisted of micro-piles of inadequate length. In Mirpur an eight storied building tilted to one side after about one year of construction. From available soil report it appeared that the building was founded on wooden piles driven in soft and organic soil. It was apparent that the designer did not take into consideration the possibility of deterioration of wooden piles with time and changes in properties of organic soils with time.
In some low lying areas of Dhaka there have been reports of tilting of four to five storied buildings during construction. Tilting results in reduction of gap between adjacent buildings and adjacent buildings may almost touched each other at the top level. In some cases buildings have completely overturned and fell on adjacent houses resulting in loss of life and property.
With Dhaka becoming a mega city with one of the highest population density we have been constructing high-rise buildings with basement excavations for car park. Most of these excavations are close to existing structures. There have been cases of improper construction practice that have resulted in unwanted ground movements causing collapse of adjacent buildings.
A photograph of one of the recent shore pile failure adjacent to Hotel Sonargaon road intersection is shown.
Are we safe? What is required to prevent the failure incidences mentioned above? A case study of some of the above failures point at several factors predominant being the quality control process followed in construction and noncompliance with National Building Code requirements in building and designing these structures. There has been much discussion on how to implement regulatory controls.
One of the most important part of construction to prevent collapse is the ground stability and control during construction. The ground condition at a site is interpreted from the soil report from a soil exploration firm. It is unfortunate that although National building Code (BNBC) codifies foundation design procedure, it does not specify the competency requirements of a soil investigation firm. As a result anyone who can drill a hole is allowed to make soil investigation and interpret soil condition. Many of the firms engaged in soil boring and sampling do not have technicians trained in field testing and soil sampling. Interpretation of soil test results require qualified geotechnical engineers. In many cases geotechnical works are interpreted and done by structural designers who may not have the requisite background knowledge for geotechnical interpretation. For a safe building it would be mandatory that all soil exploration works should be supervised and interpreted by a qualified geotechnical engineer and the foundation design should be checked and certified by a geotechnical specialist.
Comments