Jagadish Chandra Roy: Mastering the art of batik
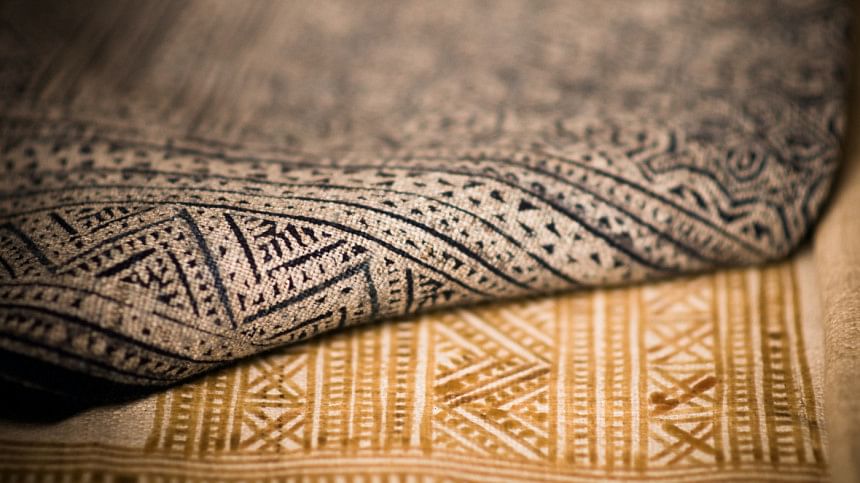
The world of fashion is constantly changing but every once in a while, someone comes up with an idea that can shake things up and change the entire dynamics of the ecosystem. Jagadish Chandra Roy may be on the verge of doing exactly that.
Over the past few years, the craftsman-entrepreneur has been consistently finding new ways to incorporate nature and natural raw materials into his ever-growing and never-ending love for the art of batik print and marketing his creations through his brand: T-gaon Craft.
Jagadish's journey with T-gaon Craft had begun way back in the late '90s when he took a course on batik during his time at Charukala.
"I was instantly drawn towards batik and out of sheer love for the art, my friends and I used to compile our works and organise exhibitions. Back then, we had to do a lot of experiments with various chemicals to see what favoured us the best. Some would not sit well while others would discolour way too easily. I used to long for better mediums and material for the work that we do," explains Jagadish.
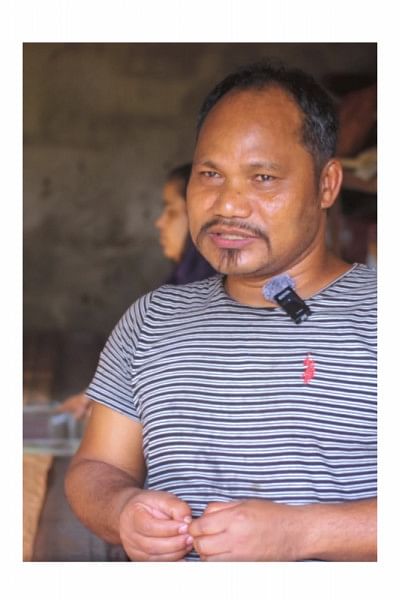
After graduating from Charukala, Jagadish got a scholarship to study in Indonesia. During his time there, he learned more about batik, experimented with newer techniques, and got a better understanding of the overall process. He wanted to apply his new skills back home.
"After returning home, I opened a small workshop where I would apply all of my knowledge to bring my ideas to life. My work would even be displayed at Jatra. However, my workshop was too far away and I was also working for UNDP at that time. So, considering all the factors, I had to briefly shut down my workshop," he lamented.
However, what did not shut down was his love for the craft and his pursuit of finding better and more sustainable techniques.
"I always saw a lot of potential in naturally occurring materials. For instance, mud stains are extremely hard to remove from clothing. I noticed how the wire I hung my clothes in would get rusty and once that rust got onto my white shirt, it would not come off. Nor would the extract from banana tree branches.
"Nature always has a lot to offer. On top of that, the raw materials that I used in my process at that point were always fluctuating in price. For instance, a wax material that is crucial to our process can cost up to Tk 14,000 and at this rate, not many artisans will be able to keep up with the production cost and sustain their business. So, I started experimenting," he added.
From various types of clay to rust to various types of leaves and even fruits. Jagadish has experimented extensively to see what works. Using naturally occurring resources can drastically cut down the cost of production and the final product is not only pretty but also more natural and friendlier to our skin and the environment.
He briefly explained the entire process to us, which takes around 6-7 days.
"At first, we get the fabric which is then treated with soda or compost to get rid of the starch. The fabric is then soaked in myrobalan plant extract and left to dry in sunlight. We then make a paste of iron and soil and soak the fabric in the paste and leave it for a few days. The fabric is then washed with clean water several times and this gets rid of the soil but the iron stays. We then boil the fabric in different materials depending on what colour we are aiming for," Jagadish stated.
The process might sound a bit strenuous but Jagadish's workshop produces around 30 products each week and with the correct amount of space and manpower, this output can be increased significantly.
His go-to materials include rust, dark soil, and vegetable dye and Jagadish has also switched from block printing to screen printing to make the process even more seamless. The only drawback is the weather sometimes, as the whole process is heavily reliant on the sun.
What started off as a Tk 10,000 investment has sold products worth over Tk 19 lakhs in just two years and has also garnered a lot of investment. T-gaon Craft has also accumulated a loyal fanbase and also boasts a wide variety of products ranging from saris, three pieces, bed sheets, curtains and even shoes, bags, and purses.
He has 15 individuals working under him and they are all rural women.
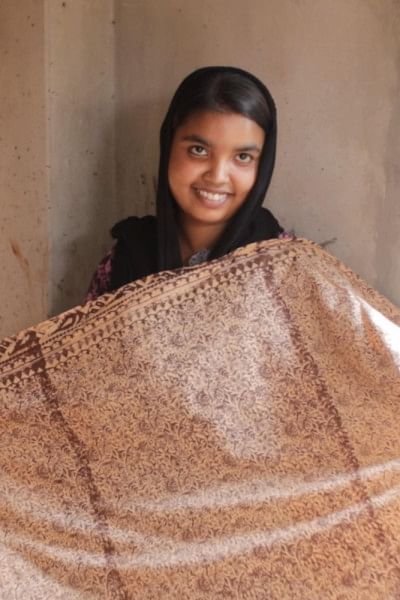
"Another beauty of this process is its inclusivity. It is very easy to learn and I have been working with various organisations to pass my knowledge to people from rural areas in hopes of creating more work opportunities," he added in his concluding notes.
Jagadish is currently conducting batik workshops at Charukala to inspire young artists. At the time of writing, he is travelling to Tangail to educate people about the benefits of using vegetable dye. In the coming days, he hopes to experiment with mahogany trees and also cactus plants. The world is quite literally his playground.
Comments