Cement: The basic building material
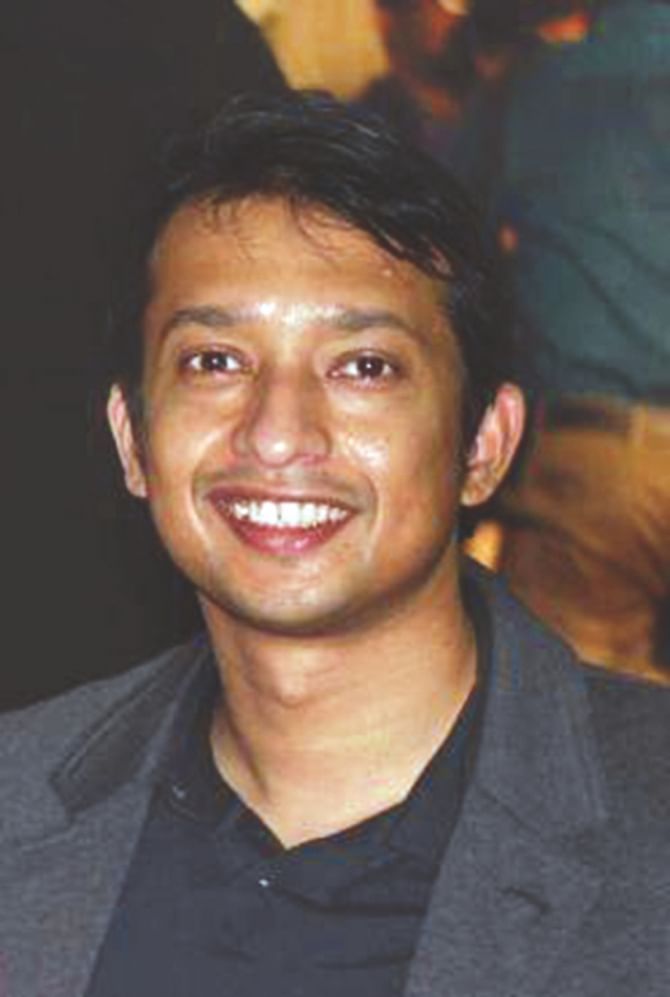
Cement is the one of the most important constituents of concrete. The function of cement in concrete is to work as a binding material. Throughout history, such binding properties of cement had played a vital role in the process of civilization. Before invention of this material, crushed masonry aggregate was mixed with calcium oxide as binder. They were used widely in the ancient world. Then the Egyptians used calcined gypsum as cement. The Greeks and Romans used lime made by heating limestone and then mixed it with sand to make mortar. They also used coarser stones to make concrete. Such cement is nonhydraulic and not resistant to water. Later, the Romans found that cement with the ability to set under water could be made, which was then used for the construction of harbours. Such cement was made by adding crushed volcanic ash to lime and was later called "pozzolanic" cement, named after the village of Pozzuoli near Vesuvius. In places where volcanic ash was scarce, such as Britain, crushed brick or tile was used instead. The Romans were therefore probably the first to manipulate systematically the properties of cementitious materials for specific applications and situations.
Today most of the structural concrete is produced by Portland cement and its various modifications. The history of Portland cement began in 1756 and such name was first patented in 1824. In Bangladesh, relative rapid growth of cement industry has been observed in mid 80s. At present, the cement industry of the country is the 40th largest market in the world. Primarily five types of Portland cement are used worldwide. However, in Bangladesh two types of cement are produced known as CEM I and CEM II. CEM I is Ordinary Portland cement (OPC) with no SCM (Supplementary Siliceous Materials such as fly ash, slag, silica fume etc.). CEM II is the Portland Composite Cement (PCC) where SCM or pozzolana is added by replacing the clinker. In areas of durability problem such as sulphate or chloride attack, PCC performs better. Before 2003, mainly OPC was used in Bangladesh. From 2003, production of Portland Composite Cement (PCC) has started in the country following the European Standard Methods (ESM). PCC gives comparable strength and durability like OPC. The basic difference between them is in the manufacturing technology. Only 65% to 80% of clinker is required to produce PCC while 95% of clinker is required to produce OPC. As a result, PCC is gaining popularity worldwide due to its environmental significance.
Clinker plays the most vital role for ensuring the strength and quality of cement. The quality of clinker must be good to get better quality cement. The four basic raw materials necessary for clinker manufacturing are calcium, silica, alumina and iron. Raw material clinker (produced by heating raw mixture of calcium, silica, alumina and iron at high temperatures) is grounded to powder and then mixed with water (Optional) and blended. Then they are burnt, and after burning gypsum is added as retarder. Addition of gypsum controls the “setting of cement”. Setting time is essential for keeping cement in plastic phase to make it workable. If gypsum is not added, the cement will set immediately after mixing with water, leaving no time for concrete placement. In addition to compound composition, the fineness of cement also affects its reactivity with water. Limits on fineness of cement are set by cost of grinding and heat evolved on hydration.

Most of the clinker used for cement production in Bangladesh is imported. Only two manufacturers produce clinker at their own plant. One is Chhatak Cement Factory Ltd a government owned company with a limited production capacity. Another one is Lafarge Surma Cement Ltd, which is situated at Chhatak, Sunamganj and produces approximate 10% of total clinker required for Bangladesh.
Clinker, the major ingredient of cement reacts in presence of water within concrete and forms calcium silicate hydrate (C-S-H gel), which actually acts as binder of aggregates in concrete. The reaction with water is called hydration process. Hydration is the primary reason for strength gaining. Rate of hydration is high in first 7 days of concrete production and consequently strength rapidly increases in early stages. Hydraulic cements (such as Portland cement) are made of a mixture of silicates and oxides, which comes from clinker. It has four main components, which are Belite (2CaO·SiO2 or C2S); Alite (3CaO·SiO2 or C3S); Celite (3CaO·Al2O3 or C3A) and Brownmillerite (4CaO·Al2O3·Fe2O3 or C4AF). Both C3S and C2S provide strength to concrete by producing C-S-H gel. However, C2S hydrates at relatively lower rates than C3S. C3A is responsible for stiffening, setting and early strength development. The amounts of these elements are adjusted during cement production to attain desired properties.
Cement industry in Bangladesh is currently in a growing phase as the consumption of cement has steadily been rising. Till now, strength is the main focus of quality related issues of cement in the country and overall quality of cement production is quite satisfactory. However, in order to ensure overall sustainability, other durability issues dependent on cement properties need to be considered. Durability of concrete infrastructures has been linked to the surrounding climatic condition of the structure. It is well known that Bangladesh is in the receiving end of the detrimental impacts of climate change. With changing climatic condition in Bangladesh, the ambient environmental conditions surrounding concrete structures may pose serious durability issues in comparison to the scenarios encountered during design phase. Therefore, the impact assessment of prevailing and future environmental scenarios on infrastructure durability is of immense importance for overall sustainable growth of the country. Future research on development of cement should address such issues related to prevailing and future environmental conditions. It is, therefore, high time for directing the focus towards other short and long term durability issues, which needs to be considered during cement production for ensuring sustainable infrastructural growth.
The writer is Assistant Professor, Department of Civil Engineering, Bangladesh University of Engineering and Technology.
Comments